ultrasonic film thickness measurement|best ultrasonic thickness gauge : manufacturer This paper focuses on available ultrasonic-based techniques for oil film thickness measurement. The organization and the main content of this review include three main areas: (a) existing models (developments and applications), (b) typical application cases, and (c) . Garçom! Olhe pelo espelho A dama de vermelho Que vai se .
{plog:ftitle_list}
Resultado da Demonstre processos de dolinamento em ação. Monte sua própria demonstração de dolina: Pegue um recipiente de plástico, como os .
ultrasonic wall thickness measurement tool
continental aircraft engine compression test
This paper focuses on available ultrasonic-based techniques for oil film thickness measurement. The organization and the main content of this review include three main areas: (a) existing models (developments and applications), (b) typical application cases, and (c) .Lubricant film thickness is the most informative variable that reflects .Lubricant film thickness measurement by ultrasonic spring model. The nature of .For optical methods an optical access to the liquid layer must be provided. .
One method that shows potential for non-invasive oil film measurement is the use .
Wear, 157 (1992) 51-64 51 Phase shift of the reflection coefficient of ultrasonic .Ultrasonic technique has been widely used in gauging the thickness of lubricant film . The liquid film stiffness was calculated by using a predicted film thickness and a bulk modulus estimated from published rheological models of lubricants under high pressure. . This stiffness governed response and resonant response can be used to determine the thickness of the liquid layer, if the other parameters are known. In this paper, .
Here, ultrasonic reflectance sensors can provide valuable transient information, as they are capable of measuring the evolution of film thickness and viscosity directly, non-invasive, and in situ .
The current developments of ultrasonic film thickness measurement technology are comprehensively reviewed in terms of theoretical models, provisional practices, and technical issues. It can be concluded that ultrasonic models have been thoroughly developed for both parallel and non-parallel structures; the temperature and pressure effect on . Ultrasonic thickness measurement can be applied to many different components and structures, and it provides a simple way to detect different problems. Some of the most common ones include: . Bio-polymers: . The measurement of oil film thickness in a lubricated component is essential information for performance monitoring and design. It is well established that such measurements can be made ultrasonically if the lubricant film is modelled as a collection of small springs. . [16] Zhang J, Drinkwater B W and Dwyer-Joyce R S 2005 Calibration of the .
ultrasonic thickness measurement tool
The main purpose of this work is to investigate the effects of the wall thickness, the ultrasonic frequency, and the acoustic impedance of wall material on the liquid-film thickness measurement by an ultrasonic pulse echo method. A series of liquid-film thickness measurements in a horizontal air-water stratified system was performed employing a plate . Jie. Zang, 2005 [55] explained three approaches to evaluate the film thickness: the time of flight, the resonant layer model, and the spring layer model. Accordingly, as seen in figure 1.31 it can . The air-coupled method were compared with a metal-side contact ultrasonic approach as well as calculating water levels in the collection tank. The falling film thickness measurement over inclined plate was used in this study. Measurement of film thickness was taken at flow rates in the range of 0.34–0.9 lpm. Ultrasonic method is promising in oil film thickness measurement, while the commonly used commercial transducers are bulky and then sometimes hinder the application of this technology in field. Using the piezoelectric element is an alternative method and has the advantage of being convenient to be fixed. In this work, the key points of the use of the .
Ultrasonic Thickness Measurement of UV-Cured Coatings on Rigid Substrates. . DeFelsko’s PosiTector 200 coating thickness gage is ideal for non-destructively measuring the dry film thickness of coatings on concrete and masonry substrates. Application Notes.
17 Ultrasonic oil-film thickness measurement From the analysis in this section, it can be seen that the ideal transducer for oil-film thickness measurement would have a high centre frequency, a small aperture size and long focal length. Figure 11 shows the performance of a possible transducer with these features i.e. fc=150 MHz, D=1 mm and F=4. . Roller bearings support heavy loads by riding on an ultra-thin oil film (between the roller and raceway), the thickness of which is critical as it reflects the lubrication performance. Ultrasonic interfacial reflection, which facilitates the non-destructive measurement of oil-film thickness, has been widely studied. However, insufficient spatial resolution around the rolling .
The measurement of oil film thickness in a lubricated component is essential information for performance monitoring and design. It is well established that such measurements can be made ultrasonically if the lubricant film is modelled as a collection of small springs. The ultrasonic method requires that component faces are separated and a reference .Title: Ultrasonic Measurement for Film Thickness and Solid Contact in Elastohydrodynamic Lubrication Author: R. S. Dwyer-Joyce; T. Reddyhoff; J. ZhuSingle-layer ultrasonic measurement is calculated using the following method: . Single-axis laser micrometers measure the thickness of film or sheet by detecting the variation of the amount of laser light passing above the product as it passes over a roller. The amount of laser light detected is inversely proportional to the sheet’s thickness. Two non-intrusive ultrasonic methods were proposed for measuring the film thickness distribution of the bearing, i.e., the full circumferential measurement and the prediction based on limited measuring points. The ultrasonic recognition model of film thickness was built. A film thickness measuring device and its calibration device were .
Through-thickness resonant frequency measurements are then used to accurately measure a thick lubricant film (h > 10 µm). These resonant frequency measurements form the starting point of the calibration. The displacement translator is then used to reduce the lubricant-film thickness into the, more practically interesting, low micron range. The possibility of the measurement of the oil film thickness by the ultrasonic method was clarified by comparing the oil film thickness with the whirling shaft of the bearing under running .
Thickness measuring is essential across many industries to monitor corrosion, erosion and damage. Ultrasonic thickness measurement (UTM) is commonly used and the method can be applied to a wide range of structures and components that includes ship hulls, piping, pressure vessels and structural steel. However, a blind region between two methods is inevitable for lubricant film thickness measurement, e.g., when using a 10 MHz ultrasonic transducer, the resonance model can calculate the thickness larger than 45 μm, while that for the spring model is less than 10 μm [34]. This is a major challenge for lubricant film thickness measurement in a . The ultrasonic technique is very effective in measuring lubricant film thickness in a noninvasive manner. To estimate the film thickness with reflection signals, two main ultrasonic models are often applied in cases of different film thicknesses; they are the spring model for thin films and the resonant model for thick films. However, when measuring oil film . The experimental apparatus shown in Fig. 4 was constructed to generate a steel–oil–steel system with a range of known oil-film thicknesses and allow measurement of the ultrasonic reflection coefficient. An oil-film (Shell Turbo T68 mineral oil) was formed between a 60×20×30 mm 3 top steel plate and a 6×20×5 mm 3 bottom steel plate. Both the bottom .
The ultrasonic method has been widely applied to measure the oil film thickness – a critical variable that reflects lubrication conditions. However, due to the thermal dependence of ultrasonic signals, significant deviations in film thickness measurements are introduced, hindering the in-situ application of the ultrasonic technique.DOI: 10.1016/J.TRIBOINT.2014.04.023 Corpus ID: 136902460; An improved ultrasonic method for lubricant-film thickness measurement in cylindrical roller bearings under light radial loadUltrasonic coating thickness gages (e.g. PosiTector 200) emit a high frequency sound pulse that travels into the coating via a coupling gel and reflects from ANY surface that is different in density.Paint thickness readings are obtained by measuring the time taken for the ultrasonic signal to propagate from the probe to the coating/substrate interface and back.Ultrasonic coating thickness measurement is now an accepted and reliable testing routine used in wood industries. The standard test method is described in ASTM D6132. “Standard Test Method for Nondestructive Measurement of Dry Film Thickness of Applied Organic Coatings Using an Ultrasonic Gage” (2022, ASTM). To verify gage calibration .
The oil film thickness in aero-engine bearing chamber influences the heat transfer capacity of the bearing chamber wall, so measuring oil film thickness accuspeedly is essential to the design and . Ultrasonic measurement for film thickness and solid contact in elastohydrodynamic lubrication. J. Tribol., 133 (2011), Article 031501, 10.1115/1.4004105. View in Scopus Google Scholar [17] K. Zhang, Q. Meng, T. Geng, et al. Ultrasonic measurement of lubricant film thickness in sliding bearings with overlapped echoes.
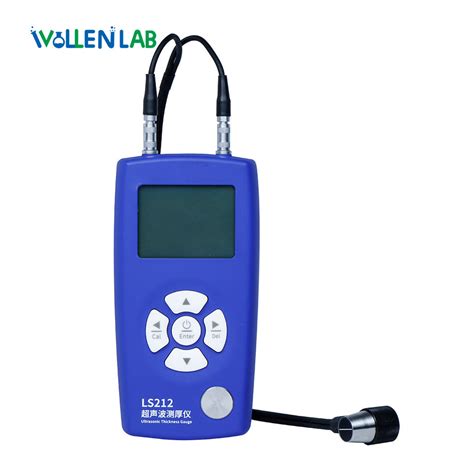
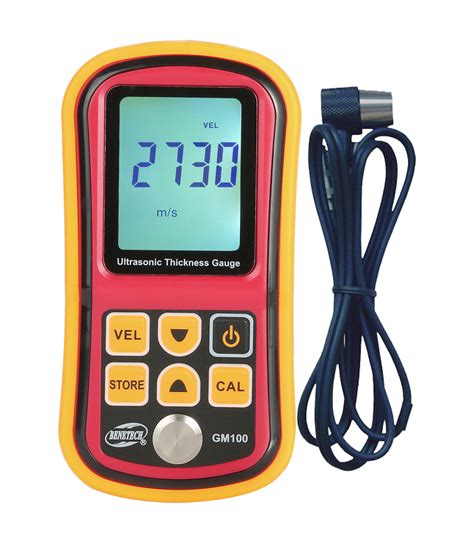
WEBConfira as notícias mais recentes que rolaram no WYD Brazuca. Nosso servidor de WYD aplica as melhores tecnologias brasileiras no clássico MMORPG Medieval com bases .
ultrasonic film thickness measurement|best ultrasonic thickness gauge